Discover What is Porosity in Welding and Its Result on Architectural Honesty
Porosity in Welding: Identifying Common Issues and Implementing Best Practices for Prevention
Porosity in welding is a pervasive concern that often goes unnoticed until it creates substantial issues with the stability of welds. This common flaw can compromise the toughness and durability of bonded structures, posing safety and security dangers and resulting in costly rework. By recognizing the origin of porosity and applying reliable prevention approaches, welders can dramatically enhance the quality and dependability of their welds. In this discussion, we will certainly explore the vital aspects adding to porosity formation, analyze its harmful effects on weld efficiency, and discuss the very best practices that can be taken on to reduce porosity event in welding processes.
Typical Reasons For Porosity
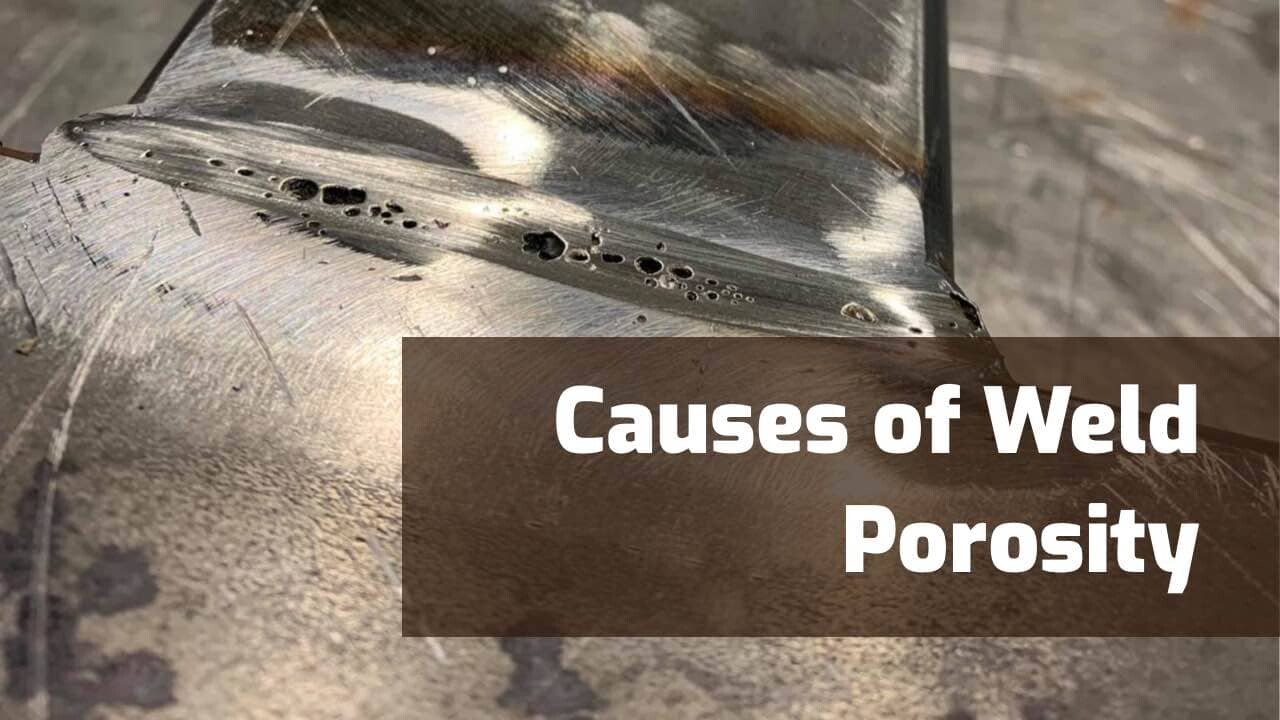
Another frequent offender behind porosity is the existence of pollutants externally of the base metal, such as oil, grease, or rust. When these contaminants are not efficiently removed before welding, they can vaporize and become trapped in the weld, causing defects. Using dirty or damp filler products can present pollutants into the weld, contributing to porosity concerns. To minimize these usual root causes of porosity, complete cleaning of base metals, appropriate securing gas selection, and adherence to optimum welding criteria are necessary methods in achieving top quality, porosity-free welds.
Effect of Porosity on Weld Top Quality

The existence of porosity in welding can significantly jeopardize the structural integrity and mechanical homes of bonded joints. Porosity produces voids within the weld metal, compromising its general strength and load-bearing capability.
Welds with high porosity degrees often tend to show reduced impact stamina and minimized capacity to flaw plastically prior to fracturing. Porosity can hinder the weld's ability to effectively transmit pressures, leading to premature weld failure and potential security threats in important frameworks.
Best Practices for Porosity Prevention
To boost the architectural stability and high quality of bonded joints, what details measures can be executed to decrease the occurrence of porosity during the welding process? Utilizing the right welding strategy for the specific material being welded, such as adjusting the welding angle and gun setting, can additionally stop porosity. Normal evaluation of welds and instant removal of any type of concerns recognized throughout the welding procedure are image source crucial techniques to protect against porosity and produce high-quality welds.
Significance of Proper Welding Techniques
Carrying out proper welding strategies is critical in ensuring the architectural stability and top quality of welded joints, constructing upon the structure of effective porosity prevention measures. Extreme heat can lead to boosted porosity due to the entrapment of gases in the weld pool. In addition, Read More Here using the proper welding parameters, such as voltage, present, and travel speed, is crucial for accomplishing audio welds with very little porosity.
Furthermore, the selection of welding process, whether it be MIG, TIG, or stick welding, must straighten with the particular needs of the project to make sure optimum results. Appropriate cleansing and preparation of the base metal, along with selecting the ideal filler product, are also necessary components of skilled welding strategies. By adhering to these best methods, welders can decrease the threat of porosity formation and create high-grade, structurally audio welds.

Testing and Quality Assurance Actions
Checking treatments are necessary to identify and protect against porosity in welding, ensuring the toughness and durability of the final product. Non-destructive testing methods such as ultrasonic screening, radiographic testing, and visual evaluation are typically employed to identify potential issues like porosity.
Post-weld assessments, on the various other hand, evaluate the last weld for any problems, consisting of porosity, and confirm that it satisfies defined standards. Executing a thorough quality control plan that consists of detailed testing procedures and assessments is vital important site to reducing porosity issues and making sure the total quality of welded joints.
Final Thought
To conclude, porosity in welding can be an usual concern that impacts the quality of welds. By determining the typical root causes of porosity and applying best practices for prevention, such as correct welding methods and testing steps, welders can make sure top quality and reliable welds. It is necessary to prioritize prevention techniques to reduce the incident of porosity and preserve the stability of welded structures.